Across the World for A Peek Inside Part of Our Supply Chain
10,000 miles from our Vermont headquarters, a van rolls down a narrow and swarming Indonesian street.
Inside there's eight: CEO Donna Carpenter, VP of Global Strategy and Insights Ali Kenney, our local Burton quality managers, and factory management. En route to evaluate one of our glove manufacturers, Ali spots the karaoke machine and talks Donna into a couple of duets. Our colleagues in the back are surprised at first, but then they join in and this whole thing breaks the ice. That's important, because in order for us to make the highest quality goods as responsibly as possible, we need to establish great relationships wherever we go.
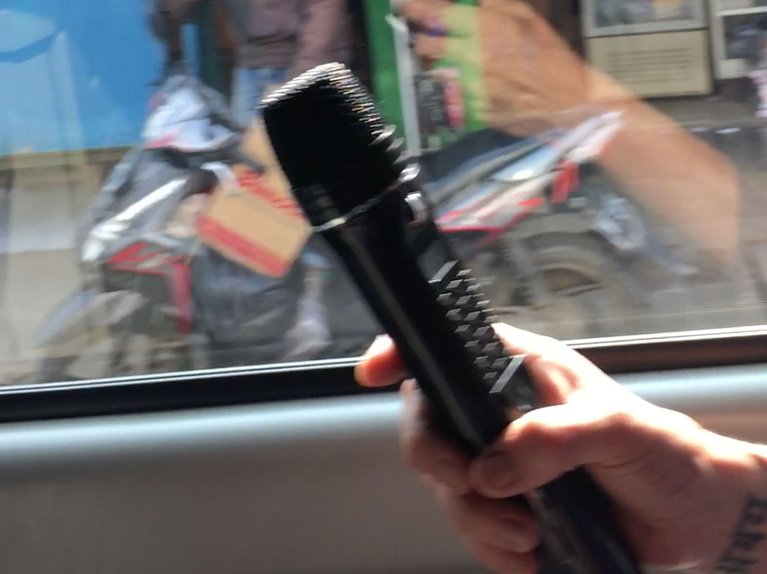
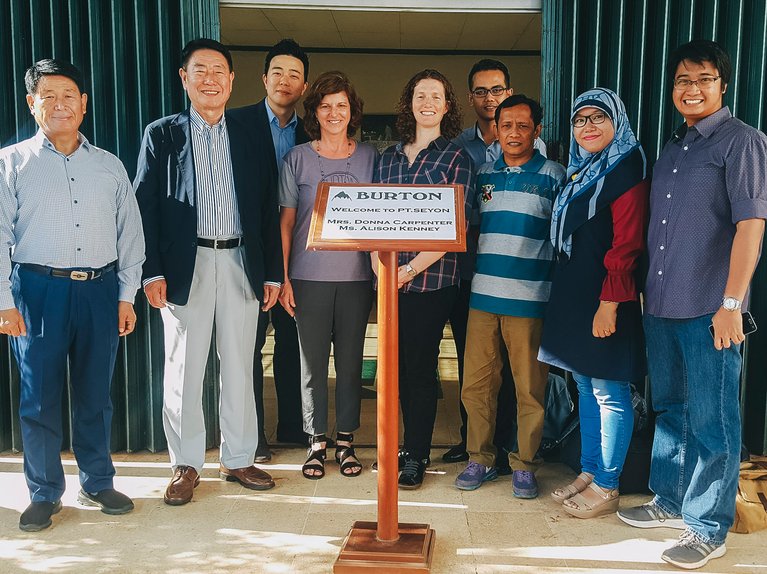
Ali's seen roughly 75 factories in the past five years, and this time Donna was determined to join. This week they'll visit five across Indonesia and Cambodia to see how they stack up against our environmental and social responsibility standards. At one point, an owner greets Donna with “I’m so happy you’re here! But...why are you here?”
Apparently there aren’t many CEOs or founders that travel across the world to check out their factories firsthand. “Because if I’m going to ensure that we uphold the highest sustainability and human rights standards, I better have seen it for myself.”
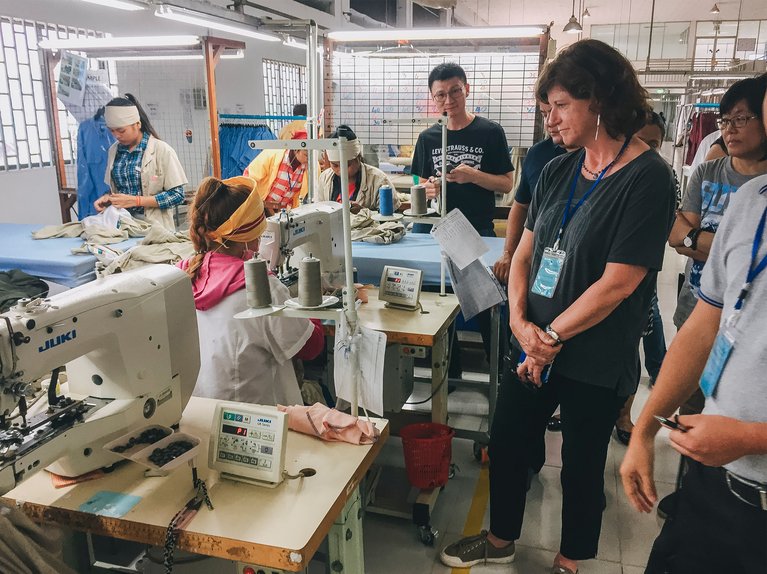
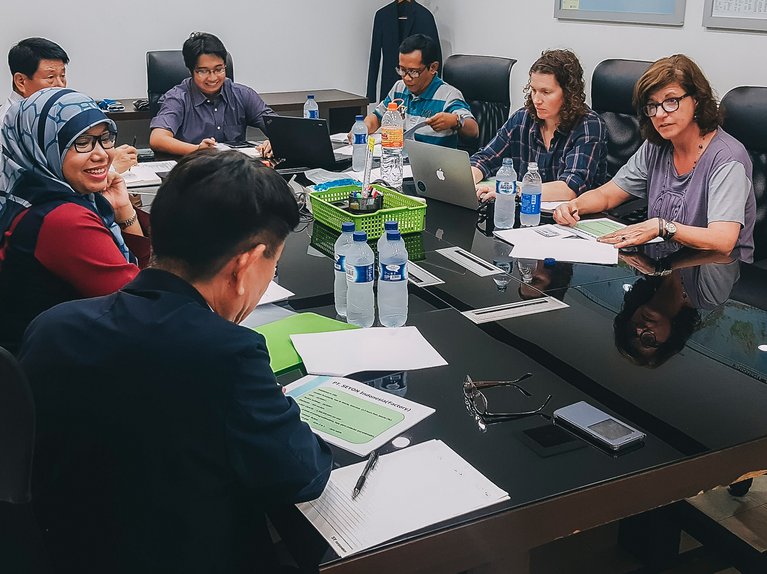
About the elephant in the room, Ali points out: “People are quick to criticize overseas manufacturing but it’s a complex topic. We look for the most specialized and high quality factories that can make product at an affordable price so that more people can get outdoors, and we can’t be xenophobes. We invest incredible amounts of resources to ensure that these factories are treating their employees and the surrounding environment responsibly. In many cases, factory jobs are one of the only ways for people to find work in these countries, and responsible companies like Burton can help drive social mobility and independence for vulnerable populations, such as women or people from poor rural communities.”
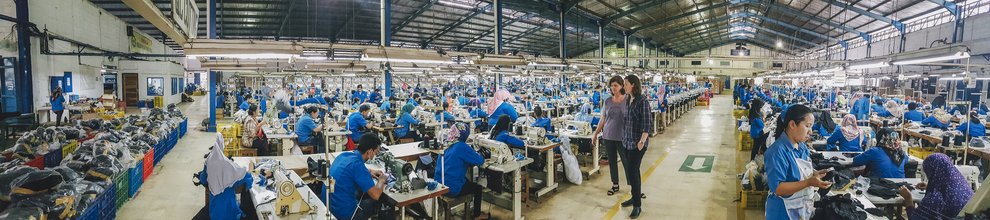
Burton's been partnering with factories all over the world for decades, but the details have drastically improved since Donna and Ali began collaborating closely many years ago. Being a privately held company and having a CEO and co-owner that's so committed to sustainability helps us to accelerate our progress beyond what we’d achieve if we were working for investors.
The work is never finished, but here's our commitment to you: We’ll continue to invest in environmental and social progress, we'll constantly raise the bar, and we'll be transparent throughout the process. The goal is to maintain what's been our pattern of progression since '77, a mission that now extends beyond Burton and asks the entire outdoor industry to improve their standards along with us.